Implementing a Lockout Management System for Streamlined Operations
- Support - Growing Your Traffic
- Dec 9, 2024
- 3 min read
Updated: Dec 10, 2024
Creating an effective Lockout Management System is critical for ensuring workplace safety and compliance in industrial environments. Such systems protect workers from the unexpected release of hazardous energy during maintenance activities and are essential for the control of hazardous energy. By establishing standardized procedures and enforcing proper training, companies can minimize overall risks and maintain a culture of safety.
At LockBoard, we understand the need for a systematic approach to implementing lockout tagout (LOTO) programs. Our solution is designed to make the process easier to follow, safer to execute, and more reliable for all authorized employees and affected employees alike.
The Importance of a Lockout Management System
The critical importance of lockout lies in its ability to protect machine operators and maintenance teams from hazardous energy sources, such as electrical energy, thermal energy, and stored energy. These energy types, if not controlled, can lead to severe injuries caused by unexpected energization or the sudden release of residual energy.
A Lockout Management System ensures that safe procedures are followed during maintenance work or repair work on dangerous machines. A key safety precaution involves identifying and labeling isolation points to secure a work area, preventing unintended start-ups during maintenance activities.
OSHA Standards and Best Practices for a Safer Work Environment
An effective system aligns with the Occupational Safety and Health Administration's (OSHA) lockout tagout standards, outlined in the Code of Federal Regulations. These regulations mandate the use of lockout devices and tagout devices to control energy sources, safeguarding the safety of workers during industrial processes.
Following LOTO guidelines and periodic inspections, combined with proper training and good practice, can ensure compliance with OSHA regulations. Training requirements must include educating both authorized employees and affected employees on safety compliance and providing the necessary information to execute LOTO procedures properly.
Regular audits and reviews of the LOTO program help reinforce best practices and allow companies to refine their standard procedures, ensuring continual improvement toward a safer work environment.
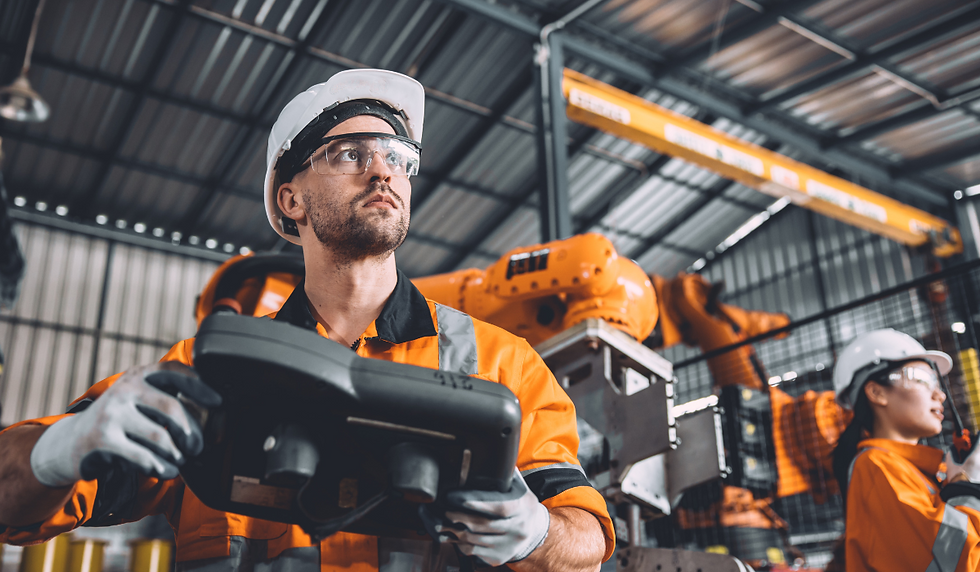
First Steps to Implementing a Lockout Tagout Program
The first step in implementing an effective lockout tagout program involves conducting a risk assessment to identify potential hazards and evaluate the power sources associated with each piece of equipment. This evaluation should pinpoint all isolation points and energy-isolating devices while documenting machine-specific lockout procedures.
The next step is to define a clear energy control procedure and assign responsibilities, including the name of the authorized person for each task. Standardized work orders provide all relevant information for proper shutdowns and lockouts during maintenance activities or repair work.
Computerized maintenance management systems (CMMS) can prove invaluable here, as they help track equipment, historical data, and compliance while streamlining energy control program execution. By integrating technology, companies can simplify the LOTO process and establish a secure work environment.

Key Components of a Lockout System
An effective lockout system includes more than just tools like LOTO devices or tagout devices; it also requires a culture of safety, proper workflows, and regular training. Prominent warning devices, such as tags or labels, must be clearly visible to alert workers about potential hazards and isolation points.
Group lockout procedures should also be established to accommodate larger teams working on complex systems like circuit breakers or equipment with multiple energy isolation devices. To maintain LOTO safety, organizations should require regular audits of lockout tagout procedures and ensure tagout compliance under the guidance of OSHA regulations and the recommendations of the American National Standards Institute.

How LockBoard Enhances Your Lockout Tagout System
When implementing or improving your lockout tagout program, LockBoard provides the ultimate solution for ease of use and safety compliance. Our lockout boards simplify the organization of LOTO devices, making it easier to enforce standard procedures and facilitate safety programs. Featuring compartments for lockout devices, tags, and documents, our boards ensure that everyone in the workplace can see where the lock box keys are.
LockBoard isn’t just a tool—it’s a commitment to worker safety and operational excellence. By incorporating our solution, your business can achieve streamlined operations, a stronger culture of safety, and effective lockout practices that protect the safety of employees, every time.
Comments